In this article, as the title suggests, I would like to write about the “interlining,” which is a crucial attachment (material) used primarily in the construction of men’s jackets.
I am Yu Yamamoto, a member of the TAILORS WORLD editorial team.
目次
About Apparel Interlining
Functions of Apparel Interlining
- Shaping and Structural Support: Interlining provides the fabric with firmness and stiffness, shaping garments beautifully and maintaining their form over time.
- Sewability: Interlining enhances the ease of sewing and ensures a neat finish.
To improve these two aspects, interlining is used. Making a garment with just fabric alone can cause it to sag and lose its shape. Interlining helps maintain the garment’s shape, and it also makes it easier to sew fabrics that might be difficult to handle alone.
Types of Apparel Interlining
While there are many types of interlining, they can be broadly categorized into the following two types:
- Sew-in Interlining: These interlinings are sewn together with the outer fabric and include haircloth interlining, shirt interlining, and more.
- Haircloth Interlining: Primarily used for the front panels of men’s suits and jackets.
- Shirt Interlining: Used for the collar, cuffs, and button plackets of dress shirts.
- Fusible Interlining: These interlinings are bonded to the outer fabric using heat from pressing machines or irons. They find extensive use in men’s clothing, women’s clothing, uniforms, and more.
About Haircloth Interlining
Examples of Haircloth Interlining Usage
Haircloth interlining is further classified into three types: “Body Interlining,” “Chest Piece Interlining,” and “Shoulder Pad Interlining.”
- Body Interlining: It serves as the foundation of the entire interlining structure, and its weight, firmness, and stiffness determine its suitability.
- Chest Piece Interlining: It provides reinforcement for the chest area and requires a stronger stiffness compared to the body interlining.
- Shoulder Pad Interlining: It further reinforces the shoulder area and is added on top of the body interlining and chest piece interlining. It requires even greater stiffness than the chest piece interlining.
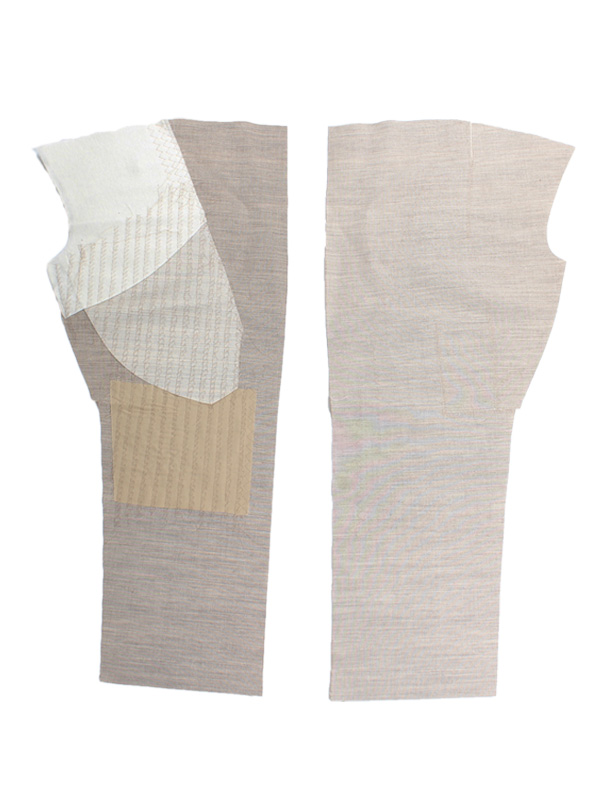
Specifications of Haircloth Interlining
Haircloth interlining is primarily used to enhance the shaping and structural support of men’s suits and jackets. When it comes to garments like suits that envelop the body, the human body has a cylindrical shape, and deformation is minimal in the warp direction due to gravity. However, deformation is more significant in the weft direction. To reinforce this aspect, haircloth interlining is designed to have stiffness in the weft direction.
Names of Processed Haircloth Interlining Parts
- Body Interlining: Used for the main body, etc.
- Chest Piece Interlining: Used for the chest area, such as chest busk interlining and shoulder padding interlining.
- Shoulder Pad Interlining: Used for the shoulder area, such as shoulder busk interlining and shoulder interlining.
- Reinforcement Interlining: Used for facing fabric, return interlining, sleeve head interlining, etc.
Manufacturing Process of Haircloth Interlining
Raw Materials
The human body has a cylindrical shape, and gravity acts in the warp direction, but the weft direction is shaped and maintained by the stiffness of the interlining. To obtain the desired stiffness in the weft yarns, coarse animal fibers are used.
Types and Characteristics of Representative Animal Fibers
- Goat Hair: Raised in the highlands of northern Greece and Macedonia, goat hair is coarse and long, known for its excellent stiffness and stiffness.
- Yak Hair: Native to the inland regions of China, yak hair is coarse and also known for its excellent stiffness and stiffness.
- Camel Hair: Found in the desert regions of Central Asia, it comes from the double-humped Bactrian camel and is particularly known for its stiffness and stiffness.
- Grey Wool: Among wool fibers, it is a coarse-grade raw wool with intermediate characteristics between hair and wool.
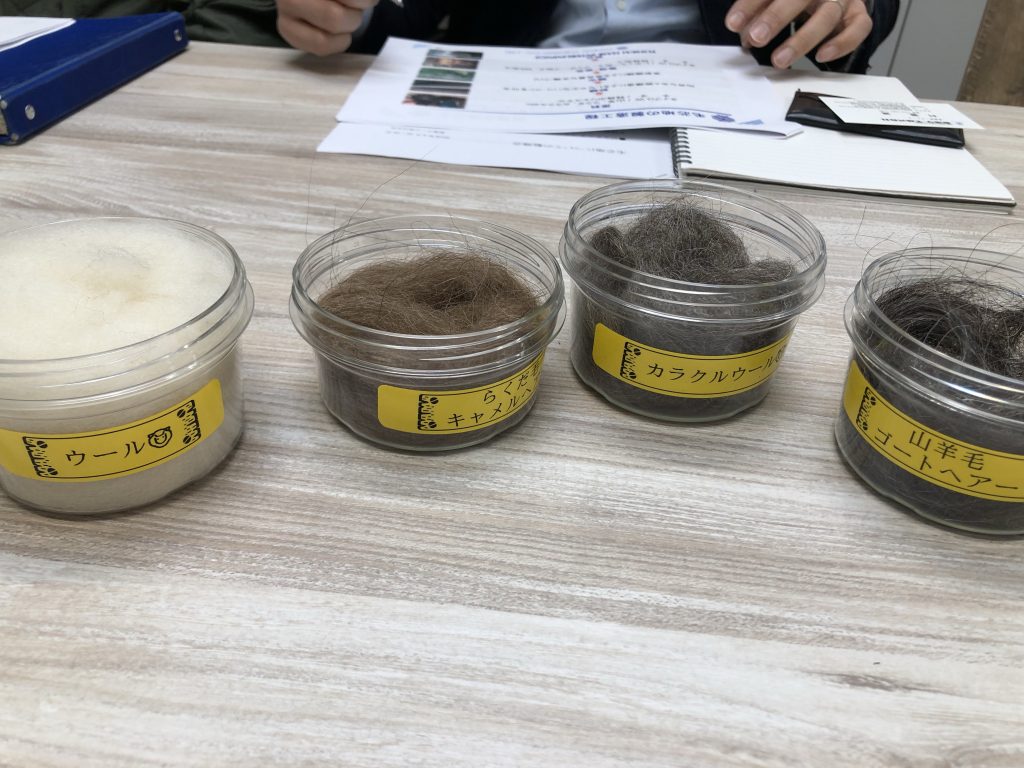
Spinning – Weft Yarn
Raw Materials: Animal fibers (goat, camel, karakul), rayon, wool, synthetic fibers Carding: Fibers are loosened, aligned, and formed into a sliver. Pre-spinning: Fibers are repeatedly mixed, combined, and stretched to achieve a consistent thickness. Fine spinning: The sliver is stretched, twisted, and wound onto bobbins to create yarn. Winding: Yarn defects are removed, and multiple bobbins are combined into one cheese.
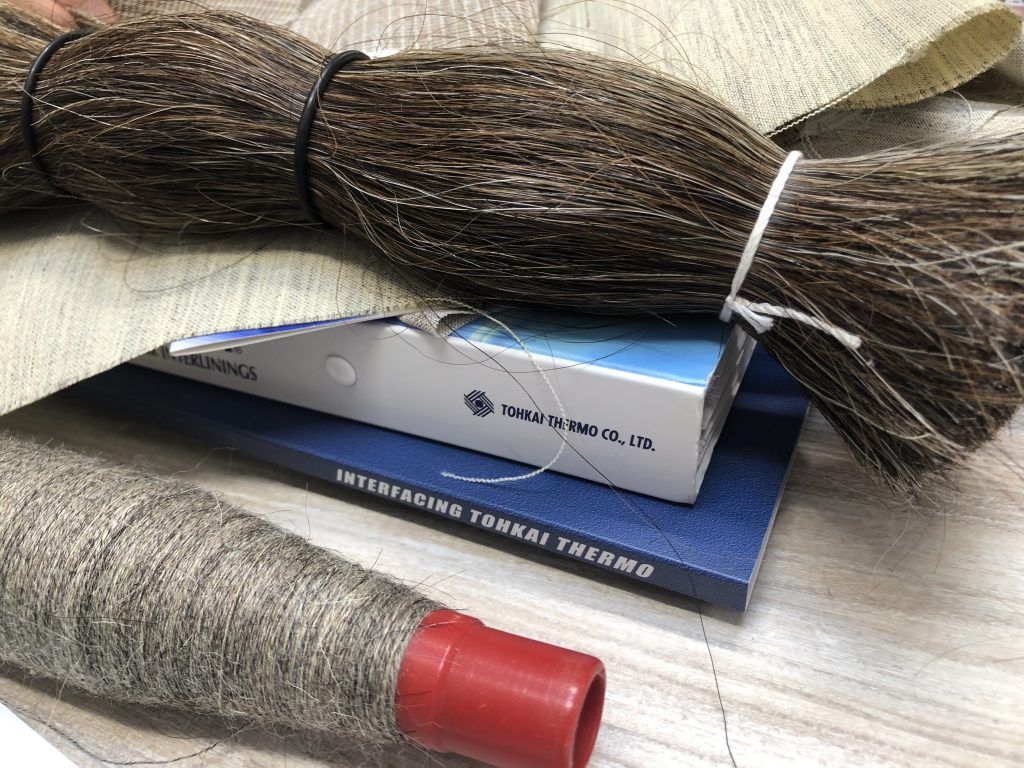
Weaving
High-quality warp preparation using innovative weaving machines Warping: Warp threads are aligned and wound onto a beam to a predetermined length and width. Weaving: Fabrics (greige) are woven on a loom according to specifications.
Finishing Processes
- Singeing: Removing surface protruding fibers (animal fibers) with a burner. *If it feels prickly, the singeing process may not have been sufficient.
- Scouring: Washing with hot water to smooth the surface and remove impurities.
- Dyeing: Mostly black dyeing; unbleached materials are not dyed.
- Drying (hot air drying)
- Padding: Applying finishing agents (shrink-proofing, texture adjustment).
- Baking: Promoting cross-linking reactions of the agents.
- Inspection: Marking and removing defects (visually by humans), followed by packaging. *It seems that the final inspection is done visually by humans.
Summary
How was it?
In this article, I have provided information about the types and manufacturing process of haircloth interlining. For orders, inquiries about haircloth interlining, accessories, or sewing services, please contact us here.
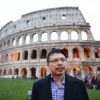
After 2 years of training at a major order-made suit store in Japan, I started my career in apparel materials and fabrics.
I’m especially good at suits and coats.