This is the first installment of our factory tour report series! We’ll delve into what we’ve learned for the first time, the production process, and more. While we couldn’t take photos of the machinery, we captured as much as we could where permitted, so get ready for a detailed report with plenty of photos!
This time, we’re focusing on polyester buttons at the Oshima Factory!
I am Yu Yamamoto, Editor of TAILORS WORLD.
目次
About Oshima Factory
Iris has a total of five domestic factories, with four in Gunma and one in Nara. Each factory produces buttons with different materials and types. The Oshima Factory in Ota City, Gunma, houses the Velga Section, where polyester resin buttons are manufactured.
What are Polyester Buttons?
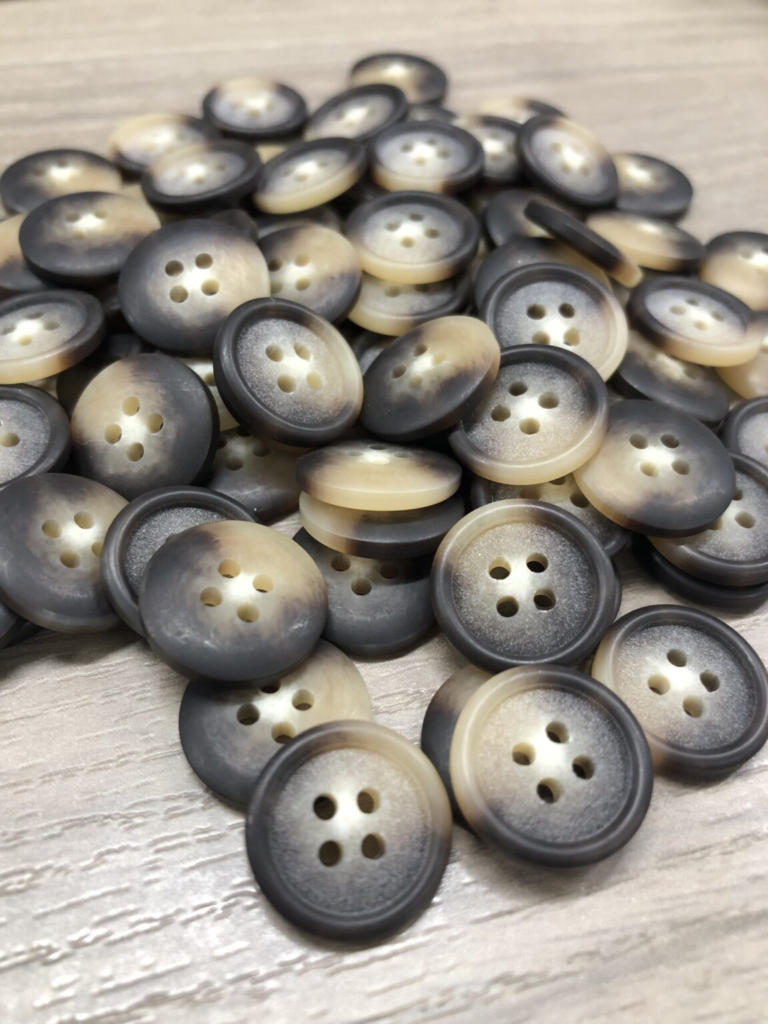
Polyester resin, derived from petroleum, is a thermosetting resin that can be processed into buttons because it can solidify at room temperature in liquid form. It boasts excellent heat resistance and chemical resistance.
In 1955, the United States developed a manufacturing technique using polyester resin to mimic the luster of shells. This technology replaced acrylic, which was previously dominant, and spread to Japan as a substitute for shell buttons. Today, polyester buttons not only dominate button manufacturing in Japan but also globally.
Polyester buttons can be molded in various natural patterns such as pearl, shell, nut, and buffalo, allowing for versatile coloration and design expressions. They can undergo secondary processes like laser engraving, dyeing, printing, and vapor deposition.
Two Methods of Manufacturing
Depending on the desired pattern, there are two molding methods:
- Rod Tube Molding Method – Suitable for patterns like buffalo, gradient, and stripes.
- Centrifugal Molding Method – Suitable for patterns like pearl, laminated buttons, and shell patterns.
Let’s dive into the manufacturing process for each method:
Rod Tube Molding
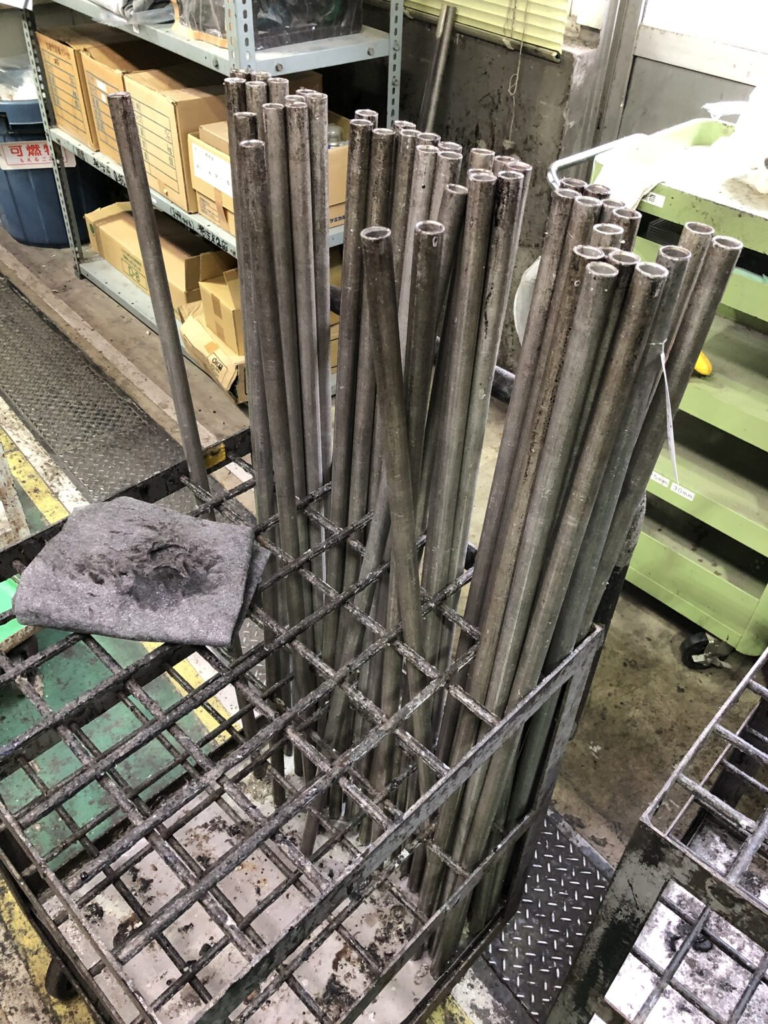
Color Mixing: Pigments are added to colorless polyester liquid along with a bit of hardener. Pouring into Pipes: The colored polyester resin is poured into aluminum pipes.
Curing: The mixture is cured in a climate-controlled room for a day.
Extraction and Cutting: The cured resin is extracted from the pipes, cut into segments, and further shaped. Roll Sorting and Finishing: The shaped buttons are sorted and finished through cutting.
Centrifugal Molding (Plates)
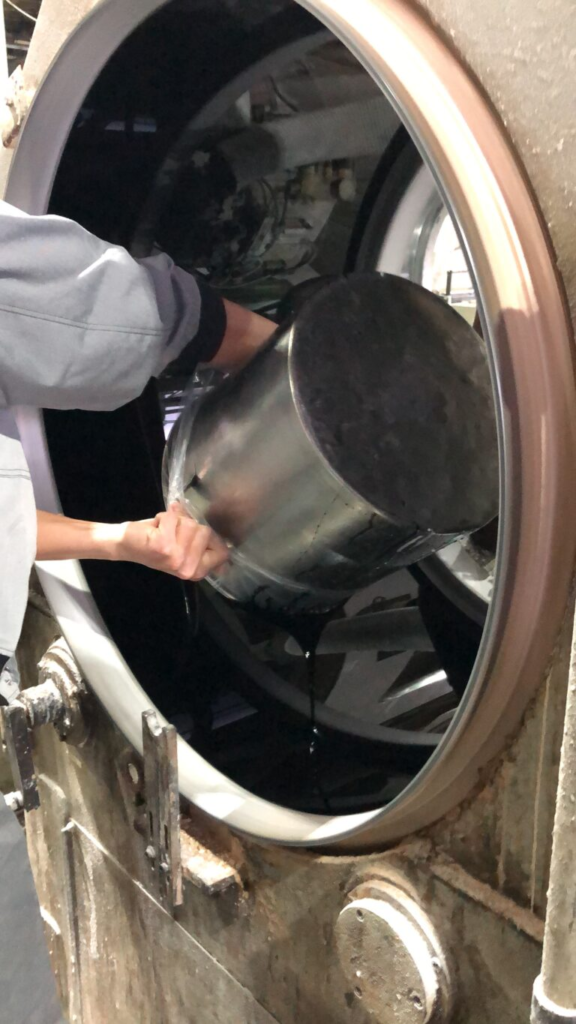
Color Mixing: Pigments are added to the colorless polyester liquid to create the desired colors.
Pouring into Drum Machines: The colored polyester resin is poured into rotating drum machines, where it solidifies into plate-shaped material. Cutting: Before complete hardening, the material is extracted, cut into plates, and further shaped using a press machine.
Common Steps
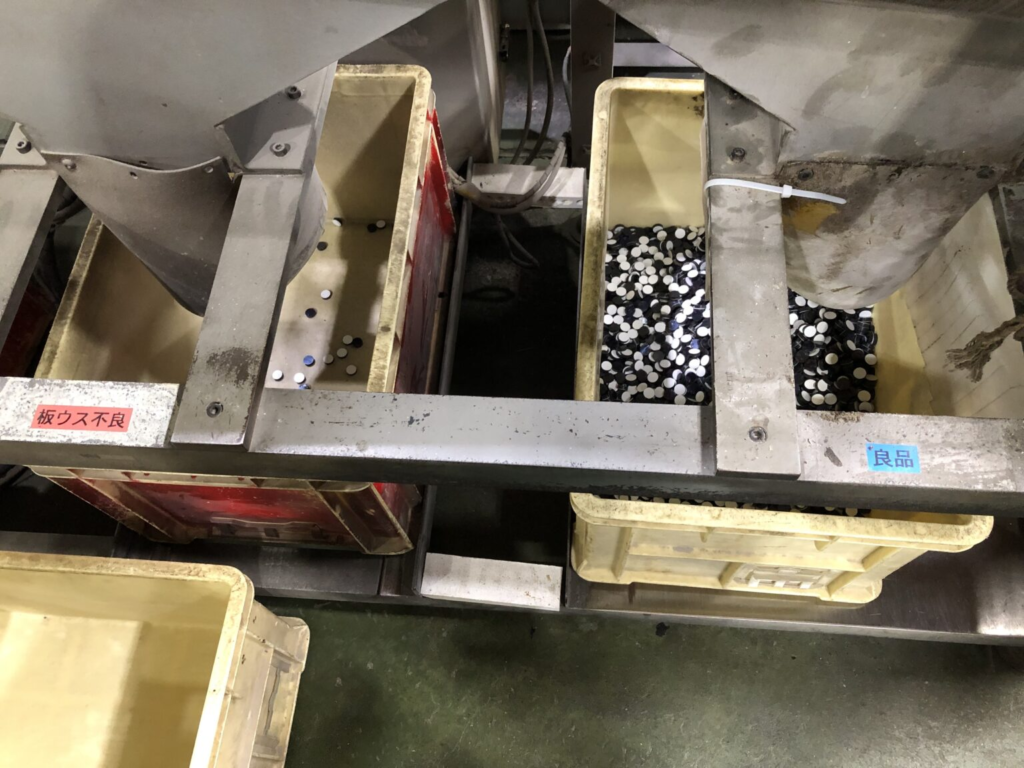
Both methods follow common steps for curing, roll sorting, and finishing. Curing is achieved either through a heat-drying machine or immersion in a large pool of hot water, depending on the color and type of button.
Inspection and Packaging
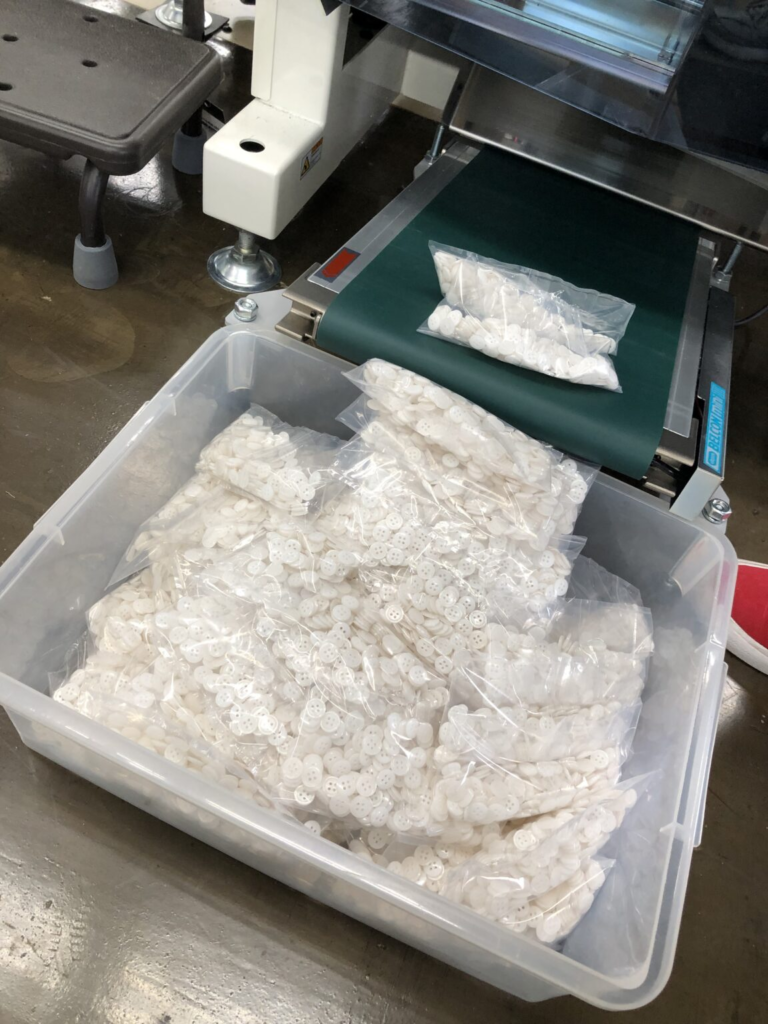
Automatic inspection machines are used for quality control, supplemented by visual inspections for some items. Buttons are then packed using machinery capable of packaging various quantities.
Conclusion
Visiting the Iris Oshima Factory and witnessing the production of polyester buttons was an enlightening experience. It’s fascinating to see the process behind everyday items that we often take for granted. Observing the manufacturing techniques has also enhanced our understanding, which we hope to apply in our future interactions with customers.
Stay tuned for our next installment, where we’ll explore the Yajima Factory and delve into metal buttons and plating processes!
For orders, inquiries related to the content above, or questions about accessories and sewing services, please don’t hesitate to contact
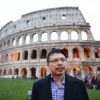
After 2 years of training at a major order-made suit store in Japan, I started my career in apparel materials and fabrics.
I’m especially good at suits and coats.